Als er één zaak hoog in het vaandel staat bij Alvance, dan is het wel veiligheid. Voor directeur Operational Excellence Koen Libbrecht mij meeneemt voor een rondleiding, moet ik eerst een hele procedure doorlopen. Nadat ik me geregistreerd heb, mag ik in een lokaaltje naar een video kijken over de veiligheidsprocedures binnen het bedrijf. Daarna dien ik een soort van examen af te leggen over hetgeen in de video verteld werd. Ik haal gelukkig de score van 70% die nodig is om verder te mogen gaan. Nog even de veiligheidsschoenen aantrekken, de veiligheidsbril en de helm opzetten, een fluohesje aantrekken en ik kan aan mijn tocht door de fabriek beginnen.
Ik stap met Koen Libbrecht langs de netjes afgebakende wandelpaden terwijl hij mij alles vertelt over de aluminiumgieterij en ik kennis mag maken met de grootste automotive koudwalserij van Europa en een CALP-lijn (Continuous Annealing Line with Pre-Treatment).
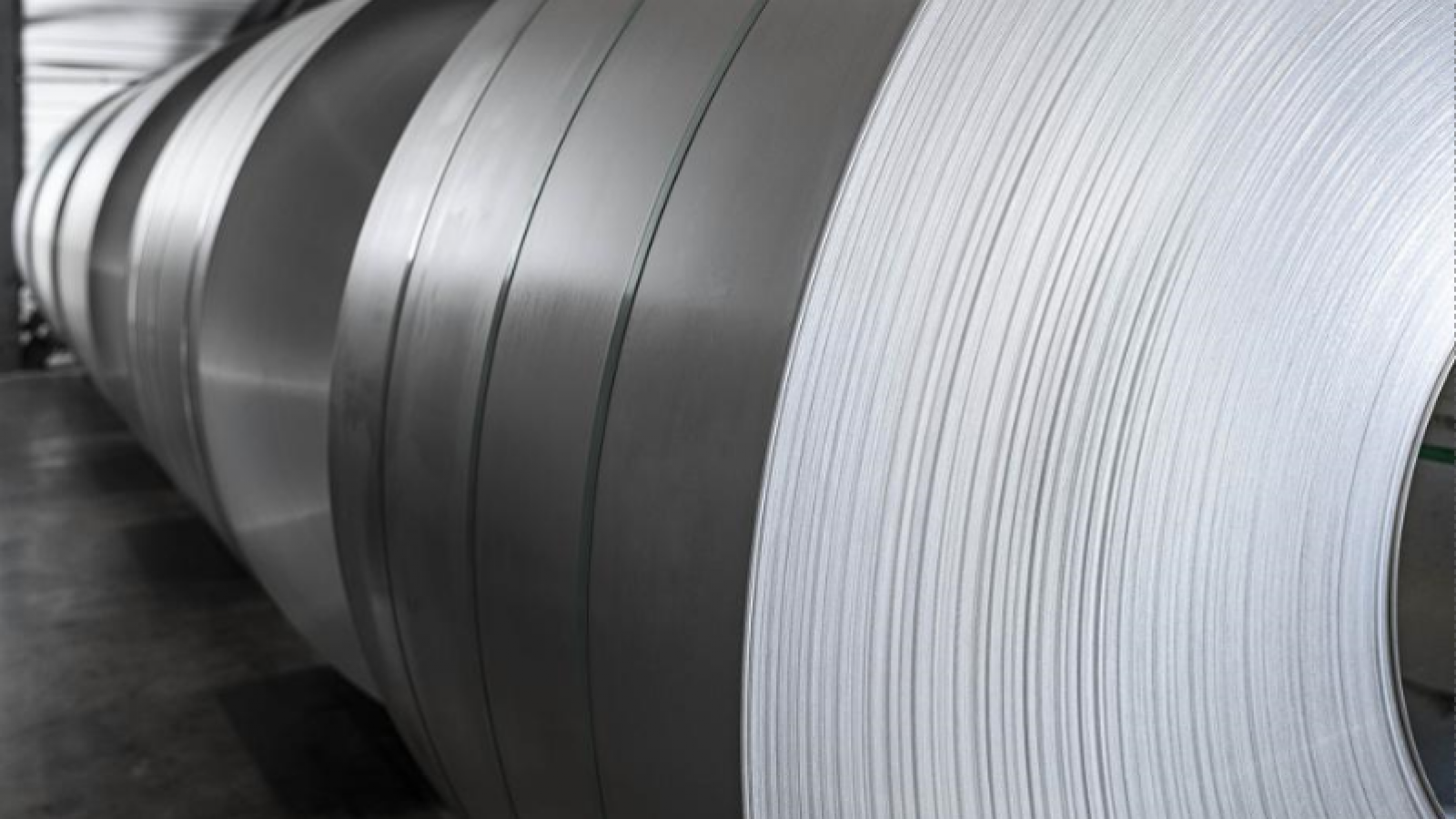
Tesla, Mercedes, Audi en BMW
Vrijwel alles wat hier gemaakt wordt, voldoet aan hele specifieke klantenwensen. De dikte, de breedte, de afwerking, … Maar liefst 200.000 ton hoogwaardig gewalst aluminium verlaat hier jaarlijks de fabriek. De ongeveer 1.000 medewerkers werken in een volcontinu ploegensysteem.
“De fabriek bestaat uit twee grote delen,” legt Koen Libbrecht uit. “We hebben een gieterij en een walserij. In de gieterij worden grote blokken aluminium gegoten. Die worden hoofdzakelijk gemaakt van gerecycleerd aluminiumschroot. De carrosserie van een Tesla, Mercedes, Audi of BMW bestaat dus voor 70 à 80% uit gerecycleerd materiaal. In wezen kan aluminium onbeperkt hergebruikt worden. De eerste keer dat aluminium gemaakt wordt in zijn eeuwigdurend leven is het natuurlijk heel zuiver. Zodra het hergebruikt wordt, komen er alsmaar meer legeringselementen in voor. Dat zijn geen ongewenste onzuiverheden, integendeel, daardoor krijgt het aluminium speciale eigenschappen. Dat betekent wel dat wanneer je aluminium gaat recycleren, je het nadien liefst voor diezelfde toepassing gaat gebruiken. Buiten de automotive sector leveren wij ook nog aluminium voor verschillende andere toepassingen. Voor het aluminium dat gebruikt wordt in de buizen voor vloerverwarming zijn wij bijvoorbeeld marktleider. We leveren geen kant-en-klare afgewerkte producten. 95% van wat hier buiten gaat, zijn grote rollen aluminium.”
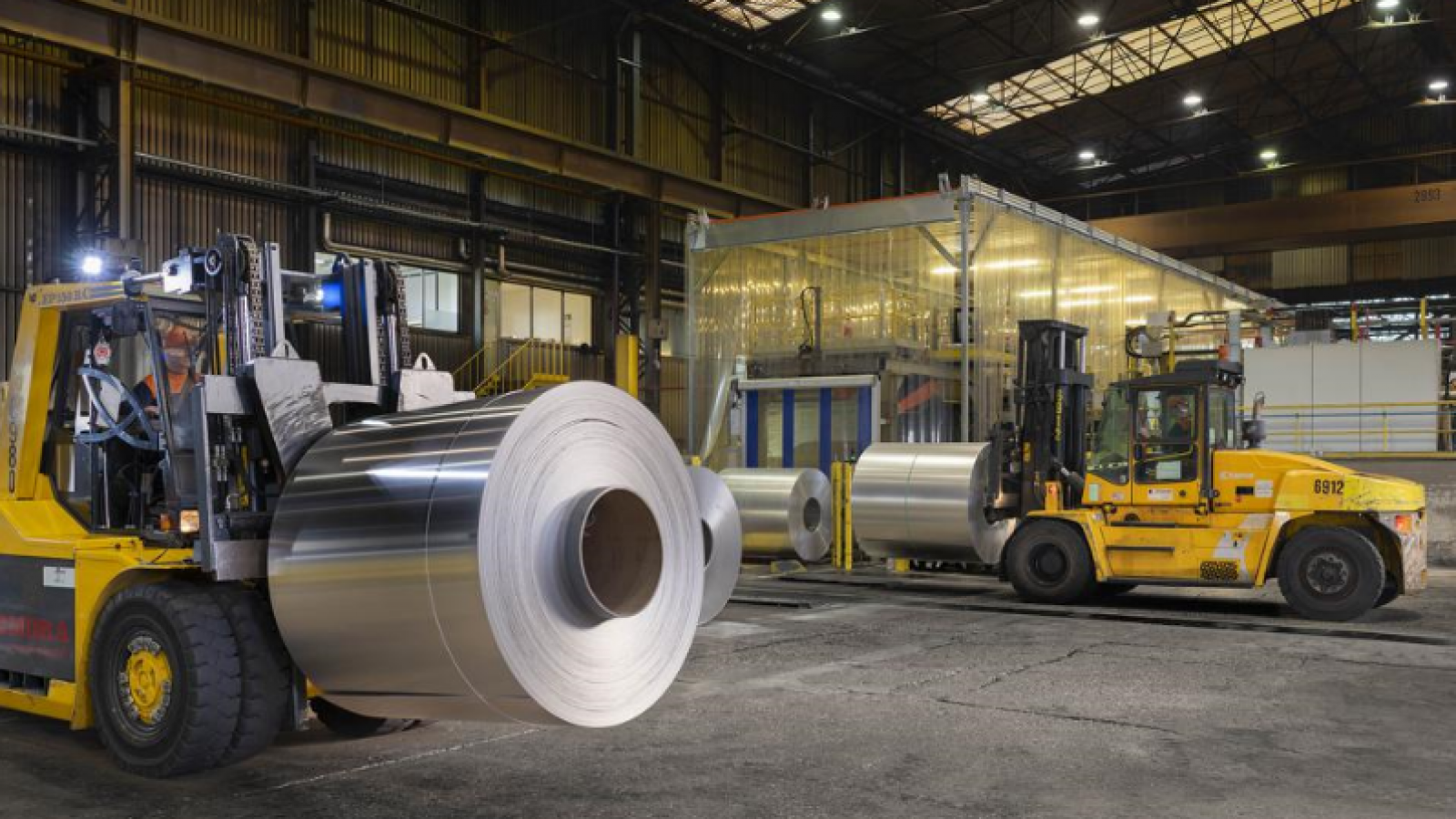
Walsen
In een grote hal liggen enorme blokken aluminium klaar om de komende dagen verder verwerkt te worden. Het zijn blokken van 4 à 5 meter lang. “Die worden opgewarmd tot 500 °C om ze daarna door de verschillende walsen te sturen. Het uiteindelijke resultaat is een rol met dunne aluminiumplaat.” Aan één van de walsen is een onderhoudsploeg bezig. Wanneer we voorbij de schakelkast wandelen, valt het mij op dat die afgesloten is met wel 20 verschillende hangsloten. “Iedereen die aan deze machine werkt moet verplicht zijn eigen hangslot aan de kast hangen. Dat betekent dat de machine pas kan heropstarten nadat elk hangslot weg is. Alleen de eigenaar van het hangslot zelf kan het verwijderen. Dat is uiteraard een veiligheidsmaatregel.”
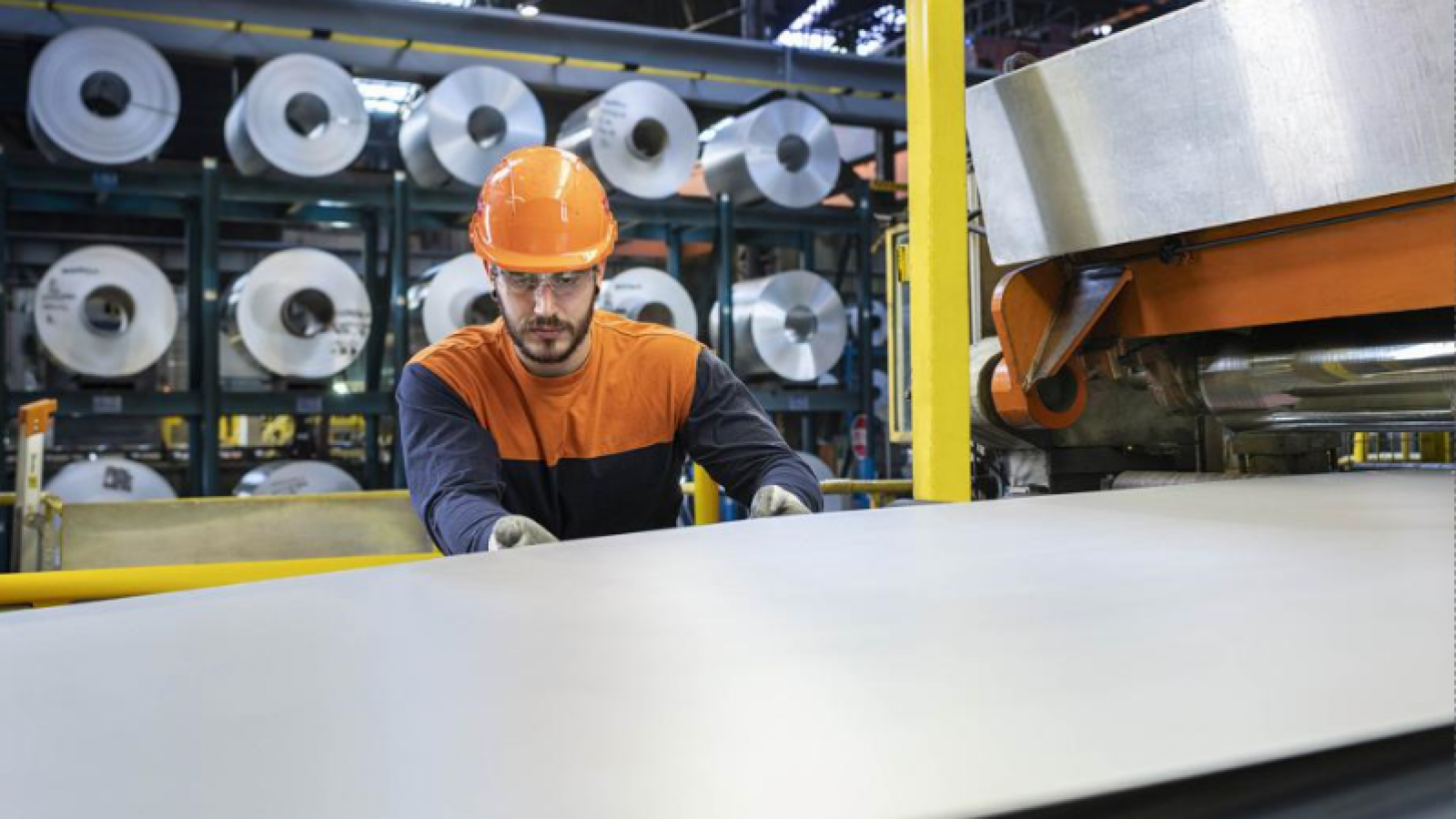
1000 meter per minuut
Koen Libbrecht toont mij de bedieningscabine van de machine. Een aantal operatoren bedienen van hieruit de machines. “Ze bepalen de snelheid en ze controleren de instellingen van heel het productieproces via camera’s. Het systeem is volledig geautomatiseerd maar toch is de taak van de walsers heel belangrijk.”
Walsen zijn grote, zware cilinders die het opgewarmde aluminium van een halve meter dik platdrukken tot een plaat van twee centimeter. Aan een volgende installatie wordt die verder gewalst tot 3 à 6 millimeter dik. Nadat ze zijn afgekoeld, zijn er nog koudwalsinstallaties die het aluminium verder afwerken tot de gewenste dikte voor de klant. De rollen aluminium worden tussen de warm- en de koudwals opgeslagen in een indrukwekkend en volledig geautomatiseerd magazijn van zeven verdiepingen hoog.
“In de bedieningskamer van de koudwals gebeurt alles automatisch, toch is er van de operatoren wat fingerspitzengefühl nodig. Je kan het vergelijken met een vliegtuig. Je hebt een automatische piloot maar je moet soms toch ingrijpen om kleine correcties te doen. De platen komen hier door de wals aan een snelheid van 1000 meter per minuut”, legt Koen uit.
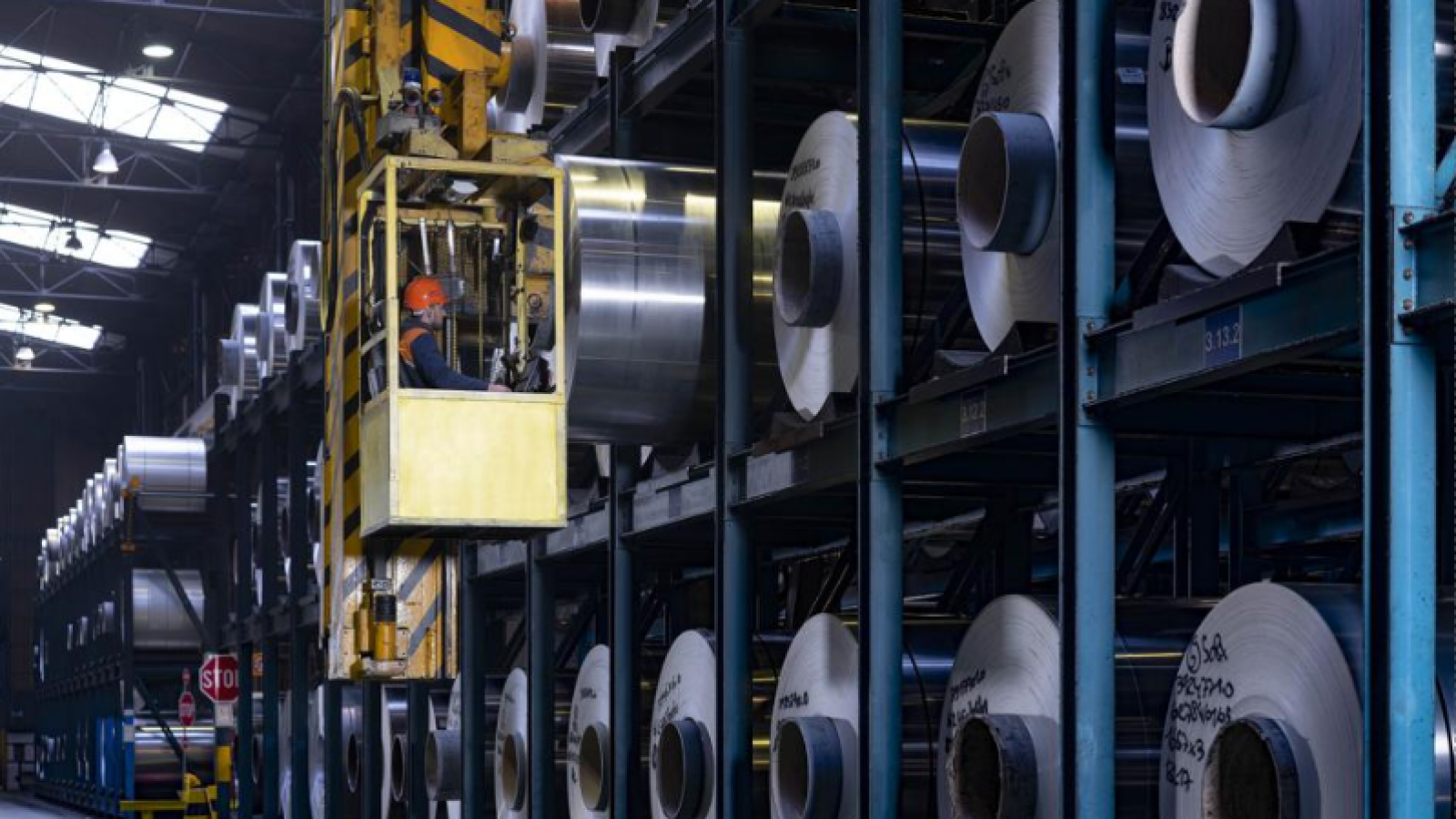
De laatste tussenstop in de rondleiding is de CALP. Dat is een installatie die de automotive producten afwerkt en ze metallurgisch geschikt maakt om verwerkt te worden in een auto. “Wat we hier doen, is het materiaal een gloeibewerking geven waardoor het in een toestand komt waardoor onze klanten het makkelijk kunnen verwerken. De allerlaatste transformatie gebeurt bij de autoproducenten zelf wanneer ze de carrosserie gaan coaten en ‘bakken’.”
Even verder passeren we bij de kwaliteitsinspectie. Met behulp van sensoren en intelligente camera’s controleren de inspecteurs nauwgezet de kwaliteit van het aluminium. “Het spreekt voor zich dat er in een carrosserie van een auto niet de minste afwijking of onregelmatigheid mag zitten.”
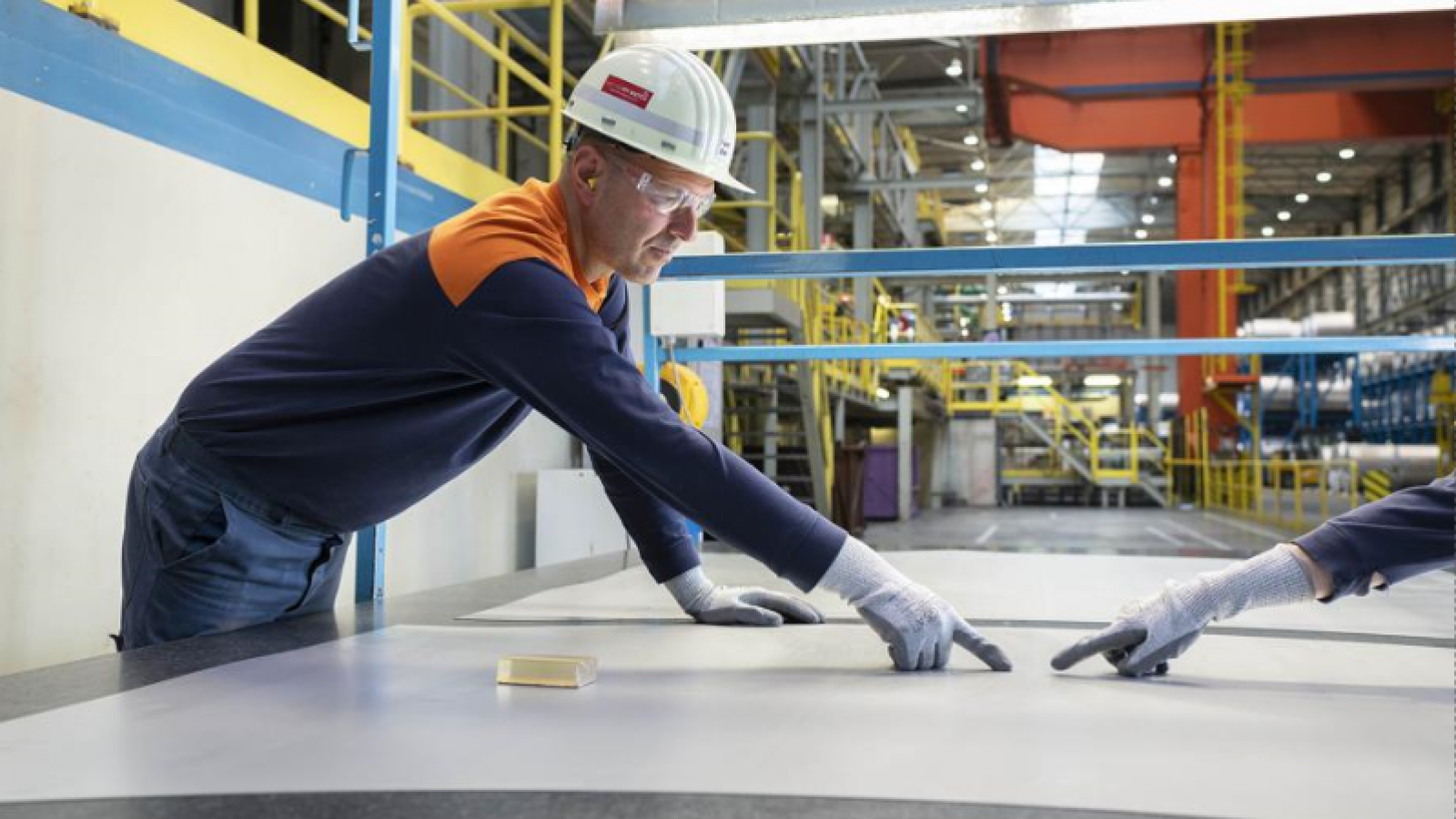
Geschiedenis
In de voorbije decennia veranderde Alvance verschillende keren van naam en eigenaar. Maar de geschiedenis van het bedrijf gaat terug tot 1946, toen Lucien Féron besloot een aluminiumverwerkingsbedrijf te starten, genaamd SIDAL (Société Industrielle de l‘Aluminium). In 1970 verwierf de Nederlandse staal- en aluminiumgroep Hoogovens Groep een minderheidsbelang in SIDAL. In 1983 volgde een volledige overname door Koninklijke Hoogovens NV. Om verdere groei mogelijk te maken, fuseerde het bedrijf in 1999 met British Steel en verandert de naam in Corus. In maart 2006 werd de aluminiumdivisie van Corus overgenomen door Aleris. In september 2020 wordt de fabriek tenslotte overgenomen door Alvance Aluminium group, onderdeel van GFG Alliance.